Hanesbrands Ergon
Establish an integrated HCM plaform to leverage Ergon analytics that improves ERP.
Egron Analytics Group
This group was established with a host of manufacturing engineers who understand the skilled line efforts and is responsible for improving the way labor is measured and calculated against standards to produce earned time used to generate payroll data. Their duties included work studies, project planning, operational standards and helping drive the data necessary for production payroll.
As a HCM Architect, I supported the Ergon Engineers with a suite of production applications that included the labor management, warehouse management, quality, payroll. HCM, Lawson, Kronos, analytics & a suite of analytics reporting designed to enhance operations, reduce costs while improving the way work is conducted on the production line. The automation that was introduced reduced the overall manual processes and increased the output for the production clerks held responsible for corrections, updates & adjustments.
My initial role was to serve as a Solutions Designer intended on refactoring their existing HCM applications was extended to the design & delivery of complete suite of solutions that embraced architectural practices that standardized the way they are built and deployed in record time & within affordable costs & time. The classical problems of poor standards, data inconsistencies, network connectivity, error handling, datasource redudancies, access controls were addressed accordingly to produce an enterprise suite of applications that faithfully adhered to the robust principles of flexibility, resilience, growth and reliability while reducing the cost of operation, including the use of production staffing to execute mundane tasks that were eventually automated.
A pliable roadmap to build a sustainable framework that traverses multiple platforms and technologies also enabled for the adoption of hybrid computing that enabled for online solutions to integrate with on-premises databases without the traditional expenses & overhead. The roadmap also provides management a clear path in operational costs & the benefits it achieves by transferring time & effort to the production staff who can now devote their time towards servicing the skill worker needs because the applications are more self-sustaining with automation in place. The development model used to build new applications became increasingly productive as proper requirements, designs & data analysis were adopted to produce far better results early into the process. Consequently, the relationship has resulted in successful adoption of new technologies that has lasted for over a decade of value driven solutions that embraces cloud, SaaS, PaaS, DaaS & hybrid computing.
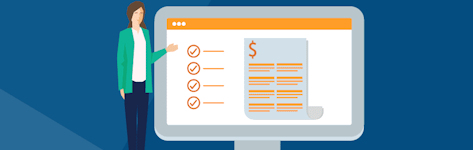
Integrated Payroll
The integrated platform & suite of applications allows HCM staff to optimize the way the evolving workforce is managed, improve vendor relationships, and support the administration to locate, allocate & resources to demands while maintaining a reasonable cost margin to meet various operational needs.
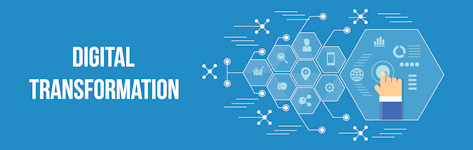
Digital Transformation
Reducing the digital footprint by offering a cloud storage & archive solutions enables the simultaneous dispositioning overhead of existing DB/2 operational platform while ensuring a suite of analytics resources are available at a reduced cost with a high-availability portal for continous processing.
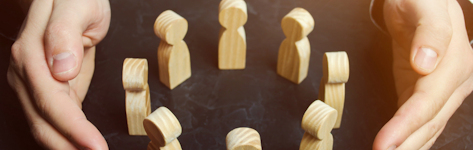
Labor Management
Emerging new technologies embracing HCM, labor & warehouse management requires a set of solutions that can consume integrated data between systems to support a labor management platform designed to improve the operations between various distribution centers and distinct operational databases.
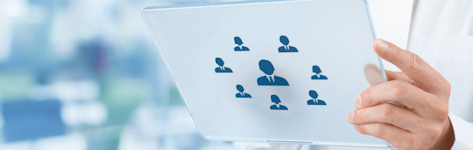
Enterprise Resource Planning
The result of CoVID-19 required safety compliance, but also the monitoring of work activities to ensure shifts contains adequate breaks, and employees are re-tasked appropriately to reduce exposure, and helped appropriate work assignments between departments, facilities & labor providers.
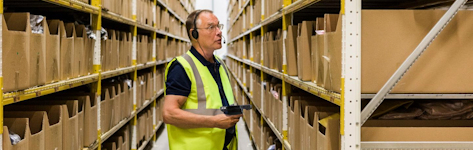
Ergon Simplification
This effort helped bridge the gaps, problems & engineering needs of various business applications into a cohesive platform to consume, process, curate data into organized structures enabling the analytics, reporting & distribution of information seamlessly across businesses with established standards.
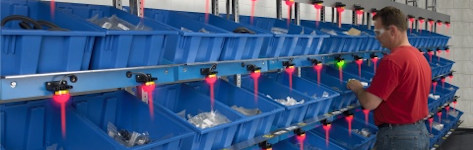
OPERATIONAL WORK STANDARDS
Reaching a degree of operational excellence is the purpose of having OWS (ISO 9001 based) business quality improvement that is able to target, tolerate and test work quality to improve work quality control, while offering a standard for production performance & measures to compute legible earned time.